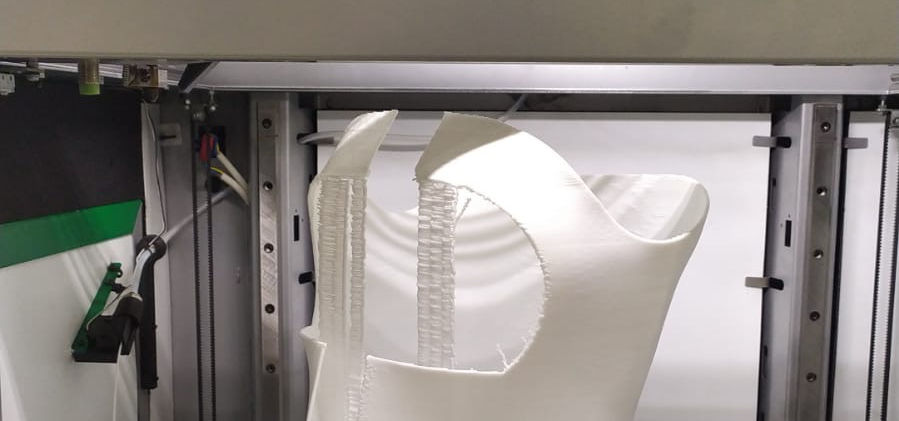
LE TECNOLOGIE UTILIZZATE
INTRODUZIONE
Nella realizzazione di un busto ortopedico di nuova generazione si utilizzano strumenti che vanno dal Reverse Engineering (acquisizione e analisi delle immagini), passando per l’ottimizzazione topologica fino alle tecnologie additive con tutti i vantaggi che queste tecnologie comportano ovvero leggerezza, personalizzazione, maggiore ecosostenibilità, riduzione dei tempi.
L’utilizzo, quindi, di tecnologie appropriate e materiali a matrice termoplastica riciclabili rappresentano un ulteriore passo in avanti verso una maggiore sostenibilità (ambientale, economica e sociale – tre dimensioni fondamentali dello sviluppo!)
TECNOLOGIE CAD/CAM
Sembra doveroso specificare quando si parla di tecnologie CAD CAM che esse si distinguono in sottrattive e additive. Nelle sottrattive un “blocco” di materiale viene, in genere, “scavato” asportando materiale e favorendo purtroppo la produzione e l’accumulo di scarti/rifiuti. Ad esempio, una lastra di poliuretano viene lavorata con la fresa per ottenere il calco su cui lavorare successivamente una lastra polimerica per ottenere il busto tradizionale. Quindi l’innovazione in questo caso sta solo nel modo in cui viene realizzato il calco ovvero si evita l’ingessatura del paziente che viene invece sottoposto a scansione per rilevare l’immagine. Nelle tecnologie additive (note nel linguaggio quotidiano come “stampa 3D”) invece non solo si evita la fase di ingessatura ma non è necessario realizzare fisicamente il calco perché si lavora “per aggiunta di materiale”, aggiungendo, cioè materiale “strato su strato” a partire da un modello digitale da cui si ottiene direttamente il modello CAD del busto da stampare.
REVERSE ENGINEERING
Il Reverse Engineering è un processo sistematico di acquisizione e analisi delle immagini, che consente di estrarre informazione di progetto da un prodotto già esistente di cui non sono disponibili modelli geometrici o digitali. Nel campo medico Risonanza magnetica per immagini (MRI) e Tomografia Computerizzata (CT) sono altre tecnologie di Reverse Engineering utilizzate per l’acquisizione dell’informazione geometrica per scopi medici. In realtà, in questo caso si utilizza uno scanner a luce strutturata che consente di ottenere l’immagine 3D su cui lavorare per la realizzazione del busto.
ADDITIVE MANUFACTURING
Il termine Additive Manufacturing si riferisce ad una famiglia di tecnologie basata su metodi CAD/CAM che consiste nel depositare - strato dopo strato (layer by layer) - strati sottili di materiale, l’uno sull’altro, producendo così dei manufatti tridimensionali anche complessi geometricamente, difficili da riprodurre con tecnologie di produzione sottrattive, ovvero con la rimozione del materiale. È per questo motivo che queste tecnologie giocano un ruolo importante nelle applicazioni della Reverse Engineering. In particolare nella FDM (Fused Deposition Modelling) si parte da un polimero TERMOPLASTICO che fluisce (quindi, da un fuso polimerico), nel senso che viene forzato ad uscire attraverso un ugello di dimensioni opportune e che si deposita sul piatto costruendo strato su strato quella particolare geometria.
MATERIALI E METODI
La procedura eseguita comprende essenzialmente queste 3 fasi
-
Scansione del paziente
-
Fase di progettazione del dispositivo che include sia la geometria sia il materiale
-
Realizzazione del dispositivo mediante tecnologia additiva scegliendo opportuni parametri di processo
La scansione viene effettuata mediante scanner a luce strutturata per acquisire l’immagine del paziente della zona interessata in poco tempo e senza contatto. Il paziente viene sottoposto a scansione con luce strutturata. Si ottiene una nuvola di punti e dopo varie procedure di “pulizia” si ottiene il modello digitale/virtuale della parte scansionata.
A questo punto partendo dalla fase di pulizia del file ottenuto dalla scansione si ottiene il modello 3D digitale del calco del busto. Quindi si procede con la modellazione CAD del busto ortopedico seguendo un percorso di ottimizzazione topologica (che ci consente un di scegliere la distribuzione ottimale di materiale all’interno del dispositivo da realizzare – definendo cioè una distribuzione EFFICIENTE del materiale da un punto di vista strutturale con architetture particolari, “zone piene” e “zone vuote”) basandosi sui risultati di precedenti analisi sperimentali sui materiali utilizzati e analisi teoriche/simulazioni meccaniche sul modello (Analisi FEM – Metodo degli Elementi Finiti). Si effettuano eventuali correzioni in FASE DI PROGETTO e si scelgono i materiali appropriati nell’ambito di un ampio range (termoplastici ad alte prestazioni).
Si prepara quindi il file di stampa che contiene le informazioni su tutti i parametri importanti come ad esempio temperature e velocità, utilizzando una macchina FDM si procede con la deposizione layer-by-layer del materiale fino all’altezza finale. Una volta ottenuto il pezzo si effettua pulitura dai supporti ed eventuale rifinitura. Il nostro TEAM DI RICERCA negli anni si è impegnato su diversi aspetti: dalla progettazione di «stampanti 3D» ad hoc allo sviluppo di un prodotto custom-made avanzato …passando per un iter progettuale che ha visto la realizzazione di diversi setupsperimentali di processo (due estrusori, singolo estrusore multifunzionale, motori specifici, velocità di flusso e camere termiche avanzate) e di differenti prototipi di prodotto fino ad arrivare a prodotti funzionali che sono in sperimentazione!
I VANTAGGI
In conclusione possiamo dire che i vantaggi sono molteplici:
-
Leggerezza (Sviluppo di strutture lightweight)
-
Personalizzazione & Customizzazione
-
Ecosostenibilità
-
Riduzione dei Tempi
-
Eliminazione del calco in gesso
Gli sviluppi futuri vanno verso:
-
la realizzazione di busti mediante lo sviluppo di piattaforme integrate (cioè possibilità di un’unica piattaforma con “integrazione” e “automatizzazione” di tutte le fasi– scansione, modellazione, simulazione e stampa 3D)
-
possibilità di contemplare già in fase di progetto le correzioni che attualmente sono effettuate con le pad in post lavorazione.